Effective Thermal Management Materials for Enhanced Device Performance
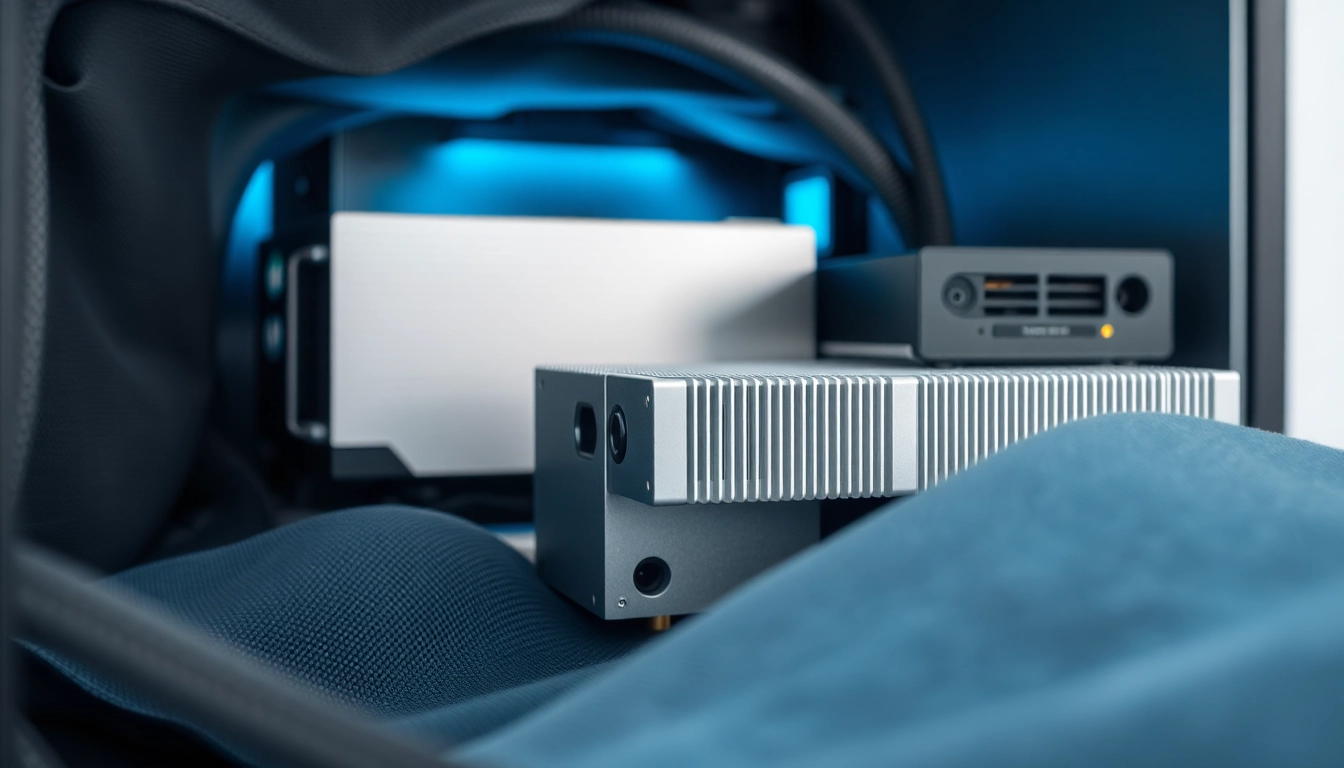
Understanding Thermal Management Materials
Definition and Importance
In today’s fast-paced technological landscape, managing heat is critical to ensuring the performance and longevity of electronic devices. Thermal management materials encompass a wide range of solutions designed to effectively dissipate heat generated by electronics. With the increasing complexity of devices and their components, understanding and implementing effective thermal management strategies becomes paramount.
Heat generation is a natural byproduct of electronic operations. As devices become smaller and more powerful, managing this heat is vital to prevent overheating, enhance efficiency, and sustain device reliability. Thermal management materials not only help in dissipating heat but also play a significant role in ensuring components function safely within their operational limits. Managing these thermal aspects can optimize performance, enhance energy efficiency, and prolong product life, making thermal management materials essential in various industries, including automotive, aerospace, consumer electronics, and telecommunications.
Types of Thermal Management Materials
Thermal management materials come in various forms, each serving unique purposes depending on the application. Here are significant categories:
- Thermal Interface Materials (TIMs): These materials improve the thermal transfer between components and heatsinks. They are crucial where thermal barriers exist due to surface imperfections. Common types include thermal pastes, pads, and greases.
- Gap Fillers: Used to fill voids between components and heatsinks, gap fillers provide essential thermal conductivity. They are often utilized where traditional flat interface materials cannot maintain contact.
- Phase Change Materials (PCMs): These materials change from solid to liquid at specific temperatures, absorbing heat during the phase change process. They can provide thermal storage and stability during high-temperature fluctuations.
- Thermal Tapes: These adhesive materials bond surfaces while providing thermal conductivity. They are commonly used for mounting components to heatsinks or enclosures.
- Heat Spreaders: Made from metals like copper or aluminum, heat spreaders distribute heat away from critical components to prevent hot spots.
Applications in Electronics
Thermal management materials are invaluable across various electronic applications ranging from consumer devices to critical high-performance equipment. Some notable applications include:
- Smartphones and Tablets: In the design of mobile devices, effective thermal management ensures that processors do not overheat, maintaining device performance and user comfort.
- Computers and Servers: PCs and data centers generate substantial amounts of heat, and optimal heat dissipation is crucial for maintaining system performance and longevity.
- Aerospace and Automotive: In automotive and avionics systems, thermal management materials are essential for ensuring electronic components remain within operational temperatures to avoid failures.
- LED Lighting: LEDs generate heat that must be managed to ensure longevity and efficiency, making TIMs and heat sinks vital components.
Key Characteristics of Thermal Management Materials
Thermal Conductivity Explained
Thermal conductivity is a pivotal property of thermal management materials, dictating their effectiveness in heat dissipation. It refers to the ability of a material to conduct heat and is typically measured in watts per meter-kelvin (W/mK). Materials with high thermal conductivity, such as copper and graphene, are employed in situations where efficient heat transfer is essential.
The choice of thermal management material often depends significantly on its thermal conductivity properties. For example, effective thermal interface materials may have conductivities ranging from 1 W/mK for generic compounds to more than 30 W/mK for advanced materials. This variation emphasizes the need for appropriate selection based on specific application requirements.
Durability and Longevity Factors
Durability is another critical characteristic, as thermal management materials must withstand environmental stressors without degrading their thermal performance. Factors influencing durability include:
- Temperature Resistance: Materials should maintain their characteristics across a range of operating temperatures.
- Mechanical Strength: Materials need to withstand physical stresses without losing their shape or thermal properties, especially in environments with vibrations.
- Chemical Stability: Resistance to oxidation, moisture, and other environmental factors can greatly impact longevity.
Environmental Considerations
As sustainability becomes a pivotal concern in manufacturing, the environmental impact of thermal management materials is increasingly scrutinized. Materials should ideally be recyclable, sourced from sustainable practices, and non-toxic. Manufacturers are more frequently turning to innovative, eco-friendly materials, such as bio-based or more environmentally benign formulations.
Choosing the Right Thermal Management Material
Evaluating Thermal Performance
Selecting the appropriate thermal management material requires thorough evaluation of its thermal performance metrics. Key aspects to measure include:
- Thermal Conductivity: As previously noted, this is essential for ensuring heat is adequately conducted away from sensitive components.
- Viscosity: Tim materials often need to be spread across surfaces. Their viscosity influences ease of application and effectiveness in filling voids.
- Thermal Resistance: This refers to the material’s ability to resist heat flow. Lower thermal resistance indicates better heat transfer.
Compatibility with Devices
Another crucial factor in selecting thermal management materials is compatibility with the devices in question. Considerations include:
- Material Composition: The selected thermal management material should not chemically react with any components it will contact.
- Form Factor: Different applications have distinct space and thickness constraints. Materials need to be design-compatible.
Cost vs Quality Analysis
Budget constraints often play a significant role in material selection for thermal management. However, it is vital to balance cost with quality; a cheaper solution may result in increased operational costs down the line due to potential component failure or inefficiency.
Innovative Solutions and Trends
Advanced Materials in Development
The advancement of thermal management materials is an area ripe with innovation. Recent developments include:
- Graphene-based materials: Owing to its incredible thermal conductivity and lightweight properties, graphene is being explored for various applications.
- Nano-enhanced TIMs: The inclusion of nanoparticles can significantly enhance the thermal conductivity of TIMs, leading to more efficient heat management.
- Smart thermal materials: Integration of sensors that can provide real-time data on temperature and heat distribution is becoming increasingly prominent.
Custom Solutions for Unique Needs
Customization of thermal management materials is becoming more commonplace, especially for specialized applications. Companies are increasingly offering tailored solutions that meet specific thermal performance and compatibility requirements for unique applications. This approach not only enhances performance but also contributes to efficiency by reducing waste.
Impact of Industry Innovations
As industries converge towards rapid technological growth, innovations in thermal management materials reflect broader trends in electronics design and manufacturing. More efficient and reliable materials are paving the way for the development of systems requiring less cooling, thus reducing energy consumption and increasing overall efficiency.
Implementation Best Practices
Installation Techniques
Effective installation of thermal management materials is crucial for maximizing efficiency. Key practices include:
- Surface Preparation: Cleaning surfaces to remove contaminants can enhance adhesion and thermal conductivity.
- Correct Application: Following manufacturer recommendations for applying materials, including layer thickness, helps maintain thermal performance.
- Pressure Application: Ensuring proper pressure during assembly can help eliminate air gaps that impede thermal transfer.
Maintenance for Longevity
Regular assessment and maintenance can enhance the longevity of thermal management systems. Considerations include monitoring temperature profiles and checking for material degradation or failure that may necessitate replacement.
Case Studies on Successful Applications
Several companies have demonstrated the successful implementation of thermal management materials. One notable case involved a high-performance computer manufacturer that utilized innovative thermal interface materials which allowed for lower operating temperatures, leading to improved performance and reduced system failures. Another example is the automotive industry, where effective thermal pads were employed to enhance the reliability of electric vehicle systems, contributing to the expansion of EV technology.
Leave a Comment