Enhancing Durability and Aesthetics with EP Coating: A Comprehensive Guide
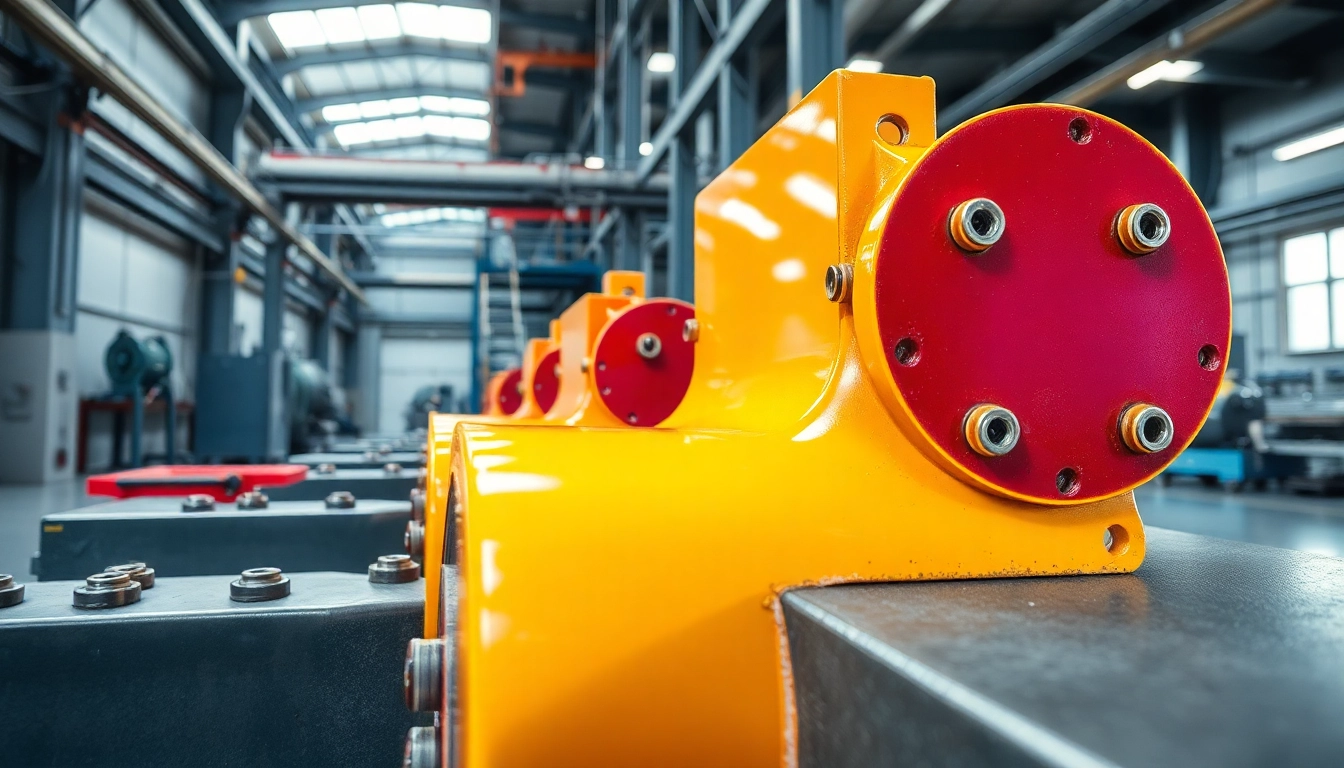
Introduction to EP Coating
Electrophoretic coating, commonly known as EP coating, is a sophisticated painting process used primarily to enhance the durability and lifespan of metal components. This technique employs electrical currents to deposit paint onto surfaces, creating a uniform and robust coating that protects against corrosion and environmental damage. As industries increasingly demand long-lasting and eco-friendly solutions, ep coating emerges as a pivotal technology across various sectors. This article explores the fundamentals of EP coating, its applications, benefits, and comparisons with other coating methods.
What is EP Coating?
EP coating, or electrophoretic coating, is a form of electrocoating also referred to simply as e-coating. It involves the use of an electric field to induce the migration of charged paint particles within a solution. These particles adhere to the surface of the substrate, effectively forming a protective film as the coating is cured. This process can be applied to various metallic surfaces, resulting in a smooth and even finish that provides excellent corrosion resistance and aesthetic appeal.
History and Evolution of Electrophoretic Coatings
The origins of electrophoretic coatings date back to the 19th century, but the technology has evolved dramatically since its inception. The modern process was developed in the 1960s and has since been refined to enhance performance and reduce environmental impact. Originally used in the automotive industry, EP coating’s versatility has led to widespread use in manufacturing, appliance production, and beyond. Engineers continue to innovate, creating formulations that cater to specific industrial needs while adhering to environmental regulations.
Applications of EP Coating Across Industries
EP coating has found applications in multiple sectors due to its unique properties. Key industries utilizing this technology include:
- Automotive: Used extensively for vehicle components to ensure corrosion resistance and aesthetic quality.
- Aerospace: Provides a robust coating for various aerospace parts, improving longevity and adherence to safety standards.
- Electronics: Offers protective layering for electronic components to guard against moisture and corrosion.
- Household Appliances: Used in washers, dryers, and other appliances for enhanced durability.
- Heavy Machinery: Protects components subjected to harsh conditions, extending service life.
Process of Electrophoretic Coating
Step-by-Step Overview of the EP Coating Process
The electrophoretic coating process involves several critical steps:
- Preparation: The surface of the substrate must be cleaned thoroughly to remove any contamination, rust, or old coatings. This is often achieved through chemical cleaning or abrasive blasting.
- Electrophoresis: The prepared parts are submerged in a liquid paint solution containing charged particles. An electric current is passed through the solution, causing the charged paint particles to migrate and adhere to the oppositely charged substrate surface.
- Curing: The coated parts are then heated in an oven to cure the paint, solidifying and enhancing the bonding of the coating to the substrate.
- Post-treatment: After curing, parts are rinsed and inspected for coating uniformity and thickness, ensuring they meet quality standards.
Essential Equipment and Materials Required
Several key pieces of equipment and materials are necessary for an efficient EP coating process:
- Coating Bath: A tank to hold the paint solution where the parts are submerged.
- Power Supply: To provide the voltage required for the electrophoretic deposition.
- Heating Oven: To cure the paint post-deposition.
- Paint Formulation: A mixture of pigments, resins, and solvents designed for electrophoretic painting.
Environmental Conditions for Optimal Performance
Environmental conditions play a significant role in the EP coating process. Key factors include:
- Temperature and Humidity: Ideal conditions depend on the specific paint formulation used and should align with manufacturer guidelines.
- Water Quality: The quality of water used in the paint bath is crucial, as impurities can impact the coating quality.
- Energization Parameters: Voltage and current must be carefully controlled during the electrophoresis step to ensure optimal deposit quality.
Advantages of Using EP Coating
Corrosion Resistance and Longevity
One of the primary advantages of EP coating is its exceptional corrosion resistance. The deposited layer is often continuous and uniform, effectively sealing the substrate against moisture and contaminants. This protective quality significantly enhances the longevity of the coated parts, making them ideal for automotive and industrial applications where exposure to harsh environments is common.
Cost-Effectiveness Compared to Other Coatings
EP coating can be more cost-effective than alternative methods, particularly when considering the reduced maintenance and replacement costs associated with durable coatings. Additionally, the efficiency of the coating process can lead to lower operational costs, as less paint is wasted compared to traditional methods.
Environmental Benefits of EP Coating Technology
EP coating techniques are generally more environmentally friendly than traditional painting methods. They produce minimal VOC (volatile organic compounds) emissions, aligning with modern regulations and sustainability goals. Moreover, the process often allows for reclaiming and reusing coating materials, further reducing waste.
EP Coating vs. Other Coating Methods
Electrophoretic Coating vs. Powder Coating
While both EP and powder coatings offer excellent durability, their application processes differ significantly:
- Application Method: EP coating utilizes an electric current to deposit a liquid paint, whereas powder coating involves the application of dry powder that is then cured under heat.
- Thickness Control: EP coatings achieve a more uniform thickness over complex geometries, while powder coatings may lead to thicker areas on edges and corners.
Performance Comparison with Liquid Coatings
Compared to traditional liquid coatings, electrophoretic coatings offer several performance advantages:
- Uniform Coverage: EP coatings can uniformly cover intricate surfaces.
- Reduced Waste: The ability to reclaim and recycle paint leads to minimal waste.
Understanding Anodizing vs. EP Coating
Anodizing is an electrochemical process primarily used for aluminum that increases corrosion resistance, while EP coating can be applied to a broader range of metals. Both methods provide protective benefits, but the choice between them often depends on the substrate material and specific application requirements:
- Material Compatibility: EP coating works on various metals, while anodizing applies specifically to aluminum.
- Coating Thickness: EP coatings often have a more consistent thickness across different substrates compared to anodizing, which can result in varying thickness levels depending on the part geometry.
Future Trends in EP Coating Technology
Innovations and Developments on the Horizon
The EP coating industry is witnessing rapid innovations focused on improving efficiency, reducing costs, and enhancing environmental sustainability. Emerging technologies, such as advancements in nanotechnology and the development of new paint formulations, promise enhanced performance and application versatility.
Sustainability and Eco-Friendly Practices in EP Coating
As sustainability becomes a central concern for many industries, EP coating continues to evolve. Efforts to minimize energy consumption during the curing process and using bio-based or waterborne formulations are on the rise, aligning with global environmental goals.
Expanding Applications in Emerging Industries
As the technology matures, the potential applications of EP coating are expanding into new sectors such as renewable energy, where durable and corrosion-resistant coatings are critical. The adoption of EP coating in the biomedical field is also being explored, particularly for devices requiring high levels of sterilization and durability.
Leave a Comment